The manufacturing sector worldwide has faced several roadblocks over the years, especially with the disruption of supply chains.
Whether caused by a hurricane or a pandemic, supply chain disruptions are becoming more frequent and severe. Using the Internet of Things(IoT) in manufacturing use cases can help reduce downtime and ensure lower disruptions.
But how?
And why is it worth your money?
To understand the benefits of IoT in the manufacturing sector, you need first to analyze the key drivers of its widespread adoption.
A key driver is traceability!
Remember that sudden breakdown in your doughing machine disrupting cookie manufacturing?
An IoT-based device can help you trace the real reason behind that breakdown in seconds.
The benefits of IoT in the manufacturing sector are not restricted to traceability and go beyond.
Despite being an attractive option for many businesses, there is skepticism! This article will discuss important aspects of using IoT in the manufacturing industry and its benefits and challenges. First, here is an overview of IoT usage in the manufacturing industry.
- The global IoT in Manufacturing Market size was valued at USD 50.0 billion in 2021 and is expected to grow at a CAGR.
- 11.9% to USD 87.9 billion by 2026.
- 12.3% to USD 122 trillion by 2029.
- Studies suggest that IoT can lead to a 20-30% increase in productivity for teams adopting automation practices.
- Studies suggest an average ROI of 200-300% for successful IoT implementations in manufacturing.
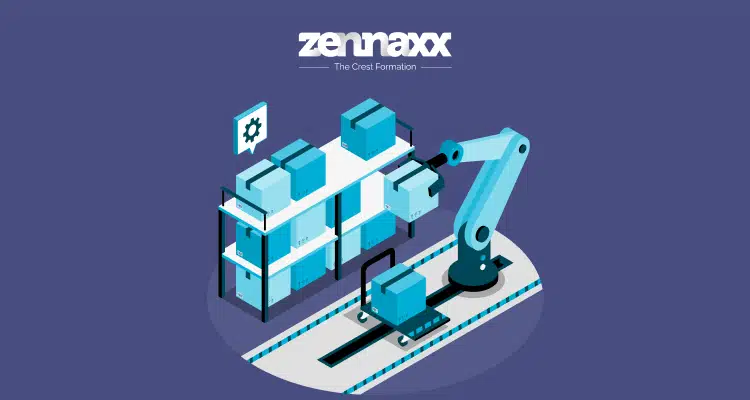
IoT in the Manufacturing Industry
IoT in the manufacturing industry is transforming digitally with the introduction of IoT devices. These devices are a network of physical objects embedded with sensors and software.
IoT devices enable manufacturing units to connect and exchange data across different equipment over the Internet. This connectivity allows manufacturers to collect and analyze valuable data remotely, improving operational efficiency, quality, and productivity.
This has led to
- Streamlined production processes,
- Real-time insights into operations
- Predictive maintenance,
- Reduced downtime
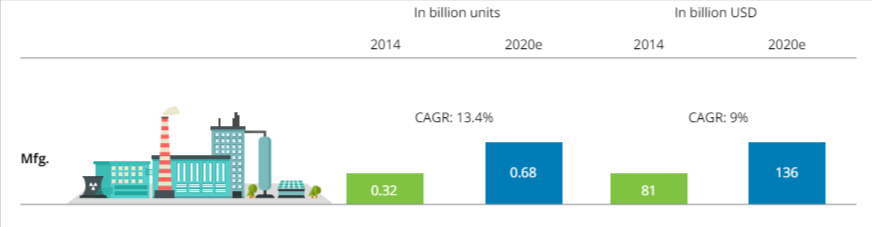
This is why the adoption of IoT in the manufacturing industry is gaining more traction, with a CAGR of 9% in revenues and 13.4% in terms of units. With a surge in IoT installations across the manufacturing industry, the key question in your mind will be,
WHY?
What’s the impact of using IoT devices in manufacturing?
Here are the answers you are looking for!
How IoT is Transforming the Manufacturing Industry
IoT devices help manufacturing plants track, trace, and rectify key machine failures to reduce downtime. In addition to detecting equipment failures, IoT devices also help predict failures, improving maintenance efficiency.
Some key transformative use cases of IoT in the manufacturing industry are:
1. Predicts Early Malfunctions
Using IoT in manufacturing can help you detect machine malfunctions early, reduce disruptions, and increase productivity. Manufacturers can use real-time data insights to address potential issues and schedule maintenance strategically and proactively.
Predictive maintenance can help improve machine lifespans and reduce the risk of failure during operations. Further, IoT adoption streamlines production processes and facilitates remote monitoring and diagnostics, leading to informed, quick decisions.
2. Higher Margins and Customer Satisfaction Levels
Getting higher margins and achieving better customer satisfaction are two significant challenges. Manufacturing is margin-intensive, and companies take a hit if there are higher defects.
At the same time, providing customer satisfaction is also crucial to ensure there is no churn. A significant benefit of IoT in manufacturing is higher margins and better customer satisfaction, achieved through better visibility.
HOW?
Simply by offering better insights!
You have better visibility on manufacturing defects and quality issues and better inventory management.
So, fewer defects, high-quality products, and better customer satisfaction ensure better margins!
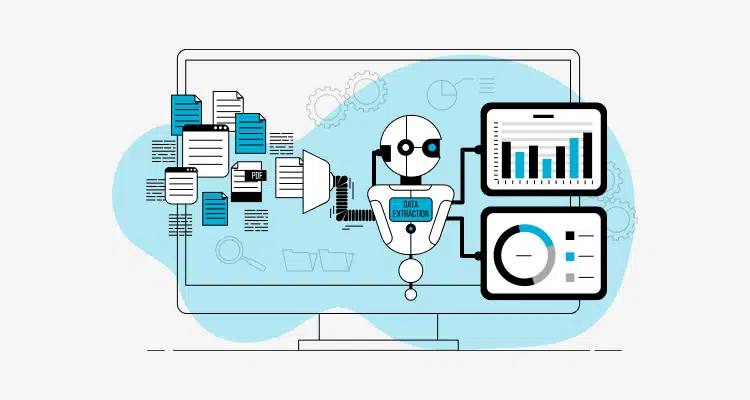
3. Improved Asset Management via Connected Supply Chain
IoT devices help track assets accurately for your supply chain operations. For example, suppose you are a manufacturing business dealing with a mass product like cars.
In that case, you need to track the accuracy of stocks, damages during delivery, and safe unloading of the vehicles.
IoT helps businesses track inventory stocks, deliveries, and asset unloading to avoid damage. One of the key benefits of IoT in the manufacturing industry is the connected ecosystem, which helps ensure seamless operations.
4. Implements Operational Intelligence
IoT enables collecting and analyzing large amounts of data from the manufacturing floor in real time.
This data-driven intelligence allows manufacturers to gain insights into every aspect of their operations, helping to optimize processes, reduce waste, and enhance productivity.
For example, if you are running a manufacturing plant for a clothing brand, operational intelligence can help identify quality issues, reduce raw material waste, and reduce maintenance costs.
5. Boosts Quality
IoT sensors and devices play a crucial role in manufacturing by constantly monitoring production processes and equipment conditions.
This provides valuable data that helps maintain operations within prescribed parameters and immediately detect deviations from quality standards.
As a result, the manufacturing of defective products is significantly reduced, and the overall quality of outputs is improved.
6. Improved Production Planning and Scheduling
A significant IoT impact in the manufacturing industry is on production planning and scheduling.
IoT devices offer real-time updates on machinery status, inventory levels, and workforce availability, making production dynamic.
The connectivity across equipment offered by IoT enables companies to use their resources more efficiently, reducing downtime and aligning production schedules with market demands.
7. Better Plant Safety and Security
IoT devices have proven effective in enhancing safety measures in the manufacturing industry.
With continuous monitoring of environmental conditions and detecting unsafe situations in real-time, alerts and trigger alarms.
For example, sensors in manufacturing plants can detect the presence of toxic gases or extreme temperatures. Upon detection, measures can be initiated to prevent accidents or injuries.
A significant benefit of IoT in the manufacturing industry is improved security systems. This includes the introduction of surveillance cameras, motion detectors, and access controls to prevent unauthorized access.
8. More Safety in Operations
IoT ensures operational safety by monitoring machinery and equipment for danger signs. Take an example of a shipbuilding yard where employees paint internal blocks within closed spaces.
Colors can have toxins that can become fumes due to a lack of oxygen, leading to unsafe operations. One of the most important impacts of IoT in the manufacturing industry is reduced accidents and injuries.
9. Predictive Maintenance
A notable benefit of IoT in manufacturing is predictive maintenance. It helps manufacturers detect potential equipment failures before they occur.
IoT devices are installed on machines that record all the important data, and using an AI-based algorithm, you can analyze data trends and anomalies.
This maintenance approach helps reduce costly downtime and extend the lifespan of machinery.
It allows you to optimize maintenance schedules and avoid unexpected repairs. It also helps you save costs and increase machine availability, which is crucial for efficient operations.
Ready to revolutionize your business with IoT technology?
Contact us now to explore how IoT can transform your business!
Exciting IoT Use Cases in Manufacturing
Innovations like IoT devices, digital twins, and remote monitoring software have significantly enhanced manufacturing efficiency.
1. Remote Monitoring
Remote monitoring is a process that involves IoT sensors that gather data from different assets, such as machinery and production lines.
Custom software then fetches this data, which helps teams monitor equipment usage and current condition.
This is especially useful in cases like the manufacturing of temperature-sensitive products.
2. Digital Twins
Digital twins are advanced virtual models replicating physical assets, processes, or systems. You can use IoT devices as digital twins to improve machine monitoring and inventory management.
You can employ internet-enabled connections with sensors and IoT devices to gather real-time data and enhance process visualization.
Manufacturers can also utilize digital twins to simulate various machining strategies, identify the most efficient methods, and optimize production lines by tracking key performance indicators.
3. Logistics Management
Using IoT in manufacturing enables real-time tracking of KPIs, enabling efficient logistics management. IoT-based software systems can also monitor and evaluate important aspects of supply chains.
It also helps optimize inventory management, analyze and improve inventory flow, and enhance the supply chain management process.
4. Manufacturing KPIs
Implementing IoT in the manufacturing industry enables manufacturers to better understand the production process. It also helps identify optimizing energy consumption, production, and inventory opportunities.
Integrating IoT sensors into the equipment allows the system to receive data and track KPIs continuously,
- Overall Equipment Effectiveness (OEE)
- Cycle time
- Throughput
- Capacity utilization
- On-Time Delivery(OTD)
- Production Schedule Attainment
- Total Cycle Time
Real-time examples of IoT in manufacturing
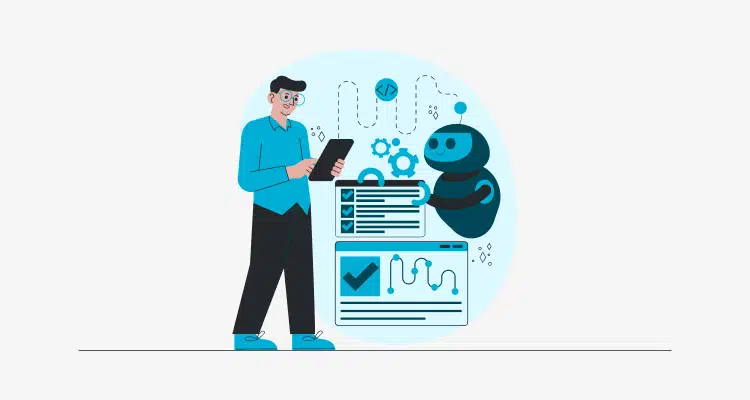
IoT technology provides real-time benefits through machine monitoring for OPE/OEE, inline QA processes, and Poka-Yoke methodologies.
Leveraging these applications, industries can effectively track and enhance equipment performance.
#1. Machine Monitoring to Track OPE/OEE
IoT in the manufacturing industry allows you to optimize production processes and improve overall equipment effectiveness (OEE). New sensors, data gateways, and software allow real-time data collection directly from machines, enhancing OEE evaluation.
Machine monitoring systems using IoT technology can also help enhance production efficiency, planning, and demand forecasting.
IoT Trends in Manufacturing for 2024
Adopting new technologies can provide numerous benefits to the manufacturing sector, including improved safety, efficiency, innovation, and cost-effectiveness.
1. Employee Safety
The integration of IoT in manufacturing focuses on improving employee safety through real-time monitoring systems.
IoT devices ensure a safer work environment for employees by constantly monitoring data.
IoT can mitigate potential safety hazards in the manufacturing environment, ensuring the well-being of workers.
Preventive maintenance based on IoT systems can help monitor equipment temperature, detect malfunctions, and predict maintenance needs.
You can proactively address safety risks, improve response times, creating a safer workplace for employees using IoT systems.
2. Security and Privacy
Manufacturers implement advanced encryption techniques and secure data protocols to safeguard sensitive information. However, maintaining cyber security can be challenging without proper monitoring.
You can prioritize security and privacy in IoT systems to protect critical data and maintain the confidentiality and integrity of information.
Incorporating advanced security measures not only helps manufacturers comply with industry regulations but also helps maintain customer trust.
3. Machine-to-Machine (M2M) Automation
IoT-enabled automation streamlines communication between machines, optimizes workflows and reduces downtime. Scheduling predictive can prevent unexpected breakdowns.
Further, autonomous data sharing and activity coordination make predictive maintenance possible.
4. IoT Blended with VR and AR Bringing Digital and Physical Worlds Closer
Blending IoT with Virtual Reality (VR) and Augmented Reality (AR) helps bridge the gap between physical and digital assets. It enhances training programs, maintenance processes, and design phases.
IoT-driven VR and AR solutions provide real-time data visualization, remote diagnostics, and step-by-step repair guidance.
Want to Automate Your Business Process With a Software Solution?
Zennaxx, a leading software development firm in Canada, has delivered 700+ bespoke solutions spanning various industries.
Challenges of IoT Adoption in Manufacturing and Business
Addressing the challenges of IoT in manufacturing and business requires careful consideration of investment risks, strategic integration, and robust security measures.
#1. Heavy Investment & Uncertainty
IoT initiatives require significant investment in hardware, gateways, and sensors. Due to the dynamic nature of IoT technologies and the unpredictable ROI, some businesses may be hesitant.
Businesses can use comprehensive cost-benefit analyses to evaluate long-term benefits. Undertaking smaller IoT pilot projects can provide insight before committing to large-scale initiatives and Implementations.
#2. Technology Integration Challenges
Integrating IoT technologies into existing manufacturing processes and legacy equipment may cause disruptions. The need for specialized skills and expertise in IoT technology can be a barrier.
However, partnering with IoT solution providers or consultants can offer valuable expertise and guidance. Investing in employee training and skill development can help address the expertise requirements.
#3. Security Concerns
IoT systems are vulnerable to cyber threats in business and manufacturing. This poses a risk to data security, privacy, and operations. Meeting regulation standards while implementing IoT is difficult but possible.
Implementing robust security protocols and adhering to comprehensive compliance frameworks are potential solutions.
#4. Legacy Equipment Integration
Compatibility issues and operational disruption can hinder the adoption of comprehensive IoT technologies.
This is due to the lack of connectivity and interoperability with legacy systems and equipment.
Retrofitting legacy systems with IoT capabilities can lead to operational disruptions and downtime, negatively impacting productivity and efficiency.
To address these issues, two potential solutions are available:
- Integrating IoT gateway devices and middleware can bridge the connectivity gap between legacy equipment and modern IoT systems.
- Phased upgrades and modernization of legacy systems can ensure seamless integration with IoT technologies without causing significant operational disruptions.
To Wrap it up!
The strategic benefits of IoT in the manufacturing industry have provided productivity boosts, cost reductions, and optimized ROI.
While there are challenges of security, technical roadblocks, and data privacy, a well-planned execution can help leverage IoT’s transformative power.
Businesses can use IoT in manufacturing to enhance predictive maintenance customizations and formulate sustainable practices.
Embracing IoT is key to staying competitive and thriving in the evolving industry ecosystem.
However, beyond the sensors and IoT device systems, you also need robust software to help analyze the data, providing deeper insights through visualizations.
This is where Zennaxx can help. We integrate IoT-based systems into your existing manufacturing units, improving ROI. So, to maximize security, productivity, and profits, get an estimate for your IoT integration project now.
Frequently Asked Questions (FAQs)
- What are the primary benefits of IoT in Manufacturing in 2024?
- IoT in manufacturing can bring many benefits, including improved operational efficiency, quality control, supply chain management, and real-time process monitoring. With IoT, manufacturers can enjoy seamless connectivity and data-driven decision-making, increasing productivity and cost savings.
- Could you provide examples of IoT use cases in the manufacturing industry?
- IoT is used in manufacturing for asset tracking, remote equipment monitoring, predictive analytics, inventory management, and automated quality control Sensors in machinery provide real-time data for proactive maintenance.
- What are the latest trends shaping IoT in Manufacturing?
- IoT is transforming manufacturing with AI/ML for predictive analytics, edge computing for real-time analysis, 5G for fast connectivity, and digital twins for optimizing production.
- How is IoT contributing to building a competitive and resilient future in manufacturing?
- IoT enables manufacturers to be more agile and flexible in production processes, improve supply chain visibility and responsiveness, foster innovation through data-driven insights, and enhance customer satisfaction through personalized products and services.
- What role does IoT play in addressing persistent industry challenges in manufacturing?
- IoT is crucial for manufacturing. It enables proactive maintenance, optimizes energy usage, improves OEE, enhances worker safety, and enables real-time inventory optimization.